Tonight I started getting my necks going. I am using the remaining peice of walnut, that I chose not to use for body wood. Having bought a 10' board, it gave me plenty of room to pick out which sections of the board I wanted to use for what. The walnut did have some small splits in it, at the end of the board. With carefulcutting, I was able to cut out peices that are just right.
To start off with, I put the board through the thickness planer. This maching will take a rough cut board, and put a nicelt planes flat surface on one side of it. If you're careful, you can get two perfectly parallel surfaces.
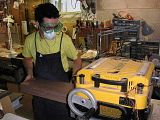
Secondly, I then cut this large board in to two boards. I ran them though my boss's joiner. A joiner will cut a perfect 90* angle to a prepped peice of wood. The joiner my boss built is made by Grizzly. It is an amazing machine.
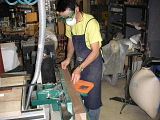
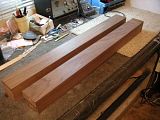
Lastly for the night, I routed my truss rod channels. The truss rod is an adjustable rod that controls the bow of the neck. Since I squared up all my edges, I chose to route the channel now, before cutting the necks out. Once cut out, I would have had to figure out some way to hold the neck down while I routed. That could be dangerous. The top, and bottom of the board get routed, because I am able to cut two necks out of each board.
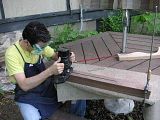