I realized today, that my body outline might not work. I plan on having the neck humbucker pick up placed right up to the end of the fingerboard, just like on a Les Paul, or PRS. The problem is that i made my contour for the lower cutaway rather close to the placement of the pickup. So I need to carefully place things out again, and possibly re-sketch my lower cutaway. It would be fine, but the pick up would be right at the edge of the guitar, and i don't think i like the idea of that. It's just a design thing. Nothing that would render the guitar unplayable.
Secondly, I duplicated the wrong template last week. It's not a big deal. I have planned this out to have back up drawings so I am constantly double checking myself as this project continues. I don't like admitting that I have made mistakes in my designs though.
Monday, January 29, 2007
Sunday, January 28, 2007
Fingerboards
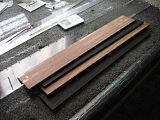
My fingerboards came in this week. I ordered 2 Honduran Rosewood, and 2 West African Ebony from Luthier's Mercantile. They come unslotted, so I had to do that myself. My boss has a table saw jig for doing this. In the pictures you first see me thickness sanding the fingerboards, then slotting them on the table saw, and finally the slotted board still attached to the slotting template.
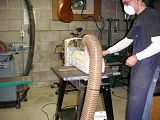
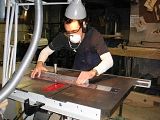
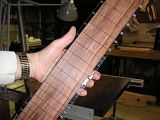
My inlay material should be in early this week.
Friday, January 19, 2007
Templates for everything
I'm still making templates. I figured out the placement of my controls too. I was initialy planning on having the bodies cut first, so I could place controls in 3-D. But I have a pretty good idea of how things will lay out from my previous guitars. This will make the cutting of wood go faster too. No stopping to make templates later on. Next week, I think I will have everything done, template wise that is.
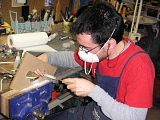
I also decided what I want to do for inlays. In the begining I was just going to have dot markers on the fingerboard. I've never been much for all the fancy blocks and paterns. But I have an idea that I think I can do quickly, and will look real nice. So now I have to buy some shell and abalone. I'll probably make the inlays before I start any wood work.
I took a picture of a 20th Anniversary PRS McCarty. It has a solid rosewood neck. The neck is oil finished, but the body still has the typical glossy finish. This is how I am planning on doing my guitars. The oil makes for a bare wood feel to the neck. The neck is protected, but not by a thick glossy finish. Many guitar players like the feeling of an oil neck, because it doesn't get gummy feeling in your hand. Just a little bonus feature I want to have with my guitars.
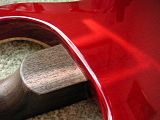
Lastly, if anyone local to me, knows of someone who would like some wood scraps for art or jewlery projects, let me know. I don't want anything to go to waste. Here's a picture of my cat sitting on my bartable. I made the table out of left over scraps from my previous guitars.
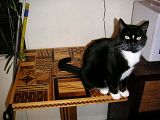
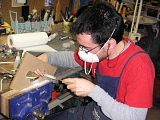
I also decided what I want to do for inlays. In the begining I was just going to have dot markers on the fingerboard. I've never been much for all the fancy blocks and paterns. But I have an idea that I think I can do quickly, and will look real nice. So now I have to buy some shell and abalone. I'll probably make the inlays before I start any wood work.
I took a picture of a 20th Anniversary PRS McCarty. It has a solid rosewood neck. The neck is oil finished, but the body still has the typical glossy finish. This is how I am planning on doing my guitars. The oil makes for a bare wood feel to the neck. The neck is protected, but not by a thick glossy finish. Many guitar players like the feeling of an oil neck, because it doesn't get gummy feeling in your hand. Just a little bonus feature I want to have with my guitars.
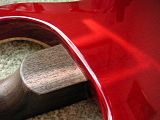
Lastly, if anyone local to me, knows of someone who would like some wood scraps for art or jewlery projects, let me know. I don't want anything to go to waste. Here's a picture of my cat sitting on my bartable. I made the table out of left over scraps from my previous guitars.
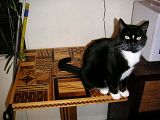
Sunday, January 14, 2007
Guitar Finish
I've decided what I will use for a finish on my guitars. Luthiers Mercantile sells what's called KTM-9. It's a water based finish, not solvent. Therefore it is environmentally friendly, but still has all the same looks, and sonic qualities of a traditional Nitro-cellulose Lacquer. Plus I can use clear epoxy as a pore filler. It all saves time, and is not detrimental to the environment. Of course if you're spraying it, you still need to use a respirator.
I'm still wood shopping. Since I last built guitars, about 4 years a go, the supply of certain woods has changed. Ebony fingerboards are about $25 now, and not slotted for fretting. Not that that is a lot of money. I can't find Water-logged.org anymore either. They used to harvest sunken logs from the bottom of Lake Superior. Sure would be nice to get a hold of some nice old growth lumber. I remember a couple customers coming into work with homemade guitars they made with wood from Water-logged. Such a shame. I wish places like that would only sell to professionals.
I'm still wood shopping. Since I last built guitars, about 4 years a go, the supply of certain woods has changed. Ebony fingerboards are about $25 now, and not slotted for fretting. Not that that is a lot of money. I can't find Water-logged.org anymore either. They used to harvest sunken logs from the bottom of Lake Superior. Sure would be nice to get a hold of some nice old growth lumber. I remember a couple customers coming into work with homemade guitars they made with wood from Water-logged. Such a shame. I wish places like that would only sell to professionals.
Tuesday, January 9, 2007
Sunday, January 7, 2007
Guitar outline
Here is a picture of the outline of my guitar design. I need to get more Plexiglas to make a template for the body. If you look closely, you can see a penciled in outline of my peghead design. I will be cutting that out this week. A duplicate will be made with the tuner holes pre-drilled, that keeps me from having to square up all the tuners on each guitar. The peghead is asymmetrical, so it would be very hard to have it come out the same each time with out the template.
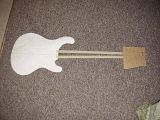
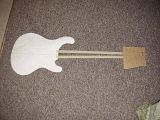
Saturday, January 6, 2007
A setback
In the photo below, you can see what was quite a let down. In one side of the walnut I was using for making necks, several tiny separations had formed over the past couple years. These little separations didn't look like much of anything. I thought I could seep some glue in through the end grain, and it would be solid. But upon further inspection, I discovered that on one of the necks, these separations were more like pockets. The wood had pulled apart, but the fibers stayed in tact. When I ran a razor blade across the top of the separation, it opened up into a sizable hole. So 2 of my necks are unusable. At some point I will patch them up with some filler strips. But they will for ever be for my use only. I can't justify taking all this time, and wanting so much for a guitar, that has had the wood patched together. Down the road, these necks will be built up for personal, experimental guitars.
Let's keep in mind my ethical stance on building/ repairing guitars. I don't want to waste wood. And when it comes to building, I try to use as much North American wood as possible. I don't want to participate in the demand of clear cutting our rain forests. There are fights between industry and environmental the time about forestry, but at least stuff harvested here, I know was done under environmental regulations. At least it is supposed to be.
So this morning I went out to shop for wood. I needed more walnut to complete the bodies, and to make up for the loss of 2 out of my 4 necks. I have gone to Youngblood Lumber (Minneapolis) in the past, and bought 3" thick walnut. That's what my necks have been cut from. But they no longer carry that size. So it was a wasted trip. I have spent the past couple hours searching the net, for another option. It gives you a sinking feeling when you shop for something particular in wood. It's just not around anymore. I did find a company in Canada that has some nice pieces. I should be able to have all the structural wood for my guitars for another $120. So that' not bad at all. I still need fingerboard wood. When it comes to fingerboard wood, exotic is about your only choice (aside from having maple fingerboards, which I don't want to do). I will most likely go with Indian rosewood. It's somewhat common, and completes a nice neck. However, on a wood suppliers website. I saw some wood called Mun Ebony (from Laos). Mostly black, with green strips in it. Very cool looking. I asked if it would be possible to get that for fingerboards.
So back to making templates. It's not as fun, but needs to be done. I still need to draw out my peghead outline.
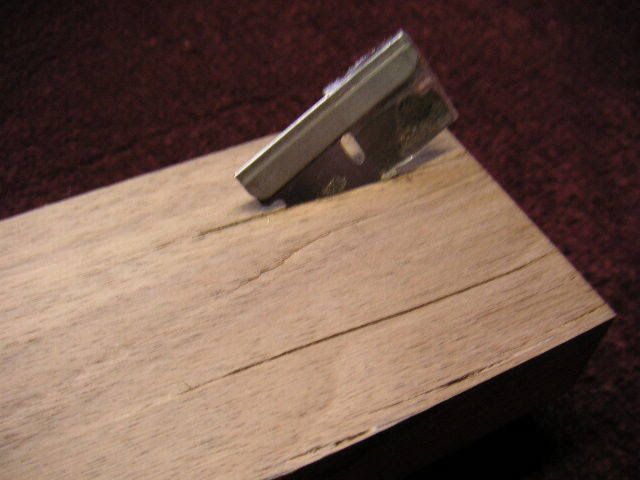
Let's keep in mind my ethical stance on building/ repairing guitars. I don't want to waste wood. And when it comes to building, I try to use as much North American wood as possible. I don't want to participate in the demand of clear cutting our rain forests. There are fights between industry and environmental the time about forestry, but at least stuff harvested here, I know was done under environmental regulations. At least it is supposed to be.
So this morning I went out to shop for wood. I needed more walnut to complete the bodies, and to make up for the loss of 2 out of my 4 necks. I have gone to Youngblood Lumber (Minneapolis) in the past, and bought 3" thick walnut. That's what my necks have been cut from. But they no longer carry that size. So it was a wasted trip. I have spent the past couple hours searching the net, for another option. It gives you a sinking feeling when you shop for something particular in wood. It's just not around anymore. I did find a company in Canada that has some nice pieces. I should be able to have all the structural wood for my guitars for another $120. So that' not bad at all. I still need fingerboard wood. When it comes to fingerboard wood, exotic is about your only choice (aside from having maple fingerboards, which I don't want to do). I will most likely go with Indian rosewood. It's somewhat common, and completes a nice neck. However, on a wood suppliers website. I saw some wood called Mun Ebony (from Laos). Mostly black, with green strips in it. Very cool looking. I asked if it would be possible to get that for fingerboards.
So back to making templates. It's not as fun, but needs to be done. I still need to draw out my peghead outline.
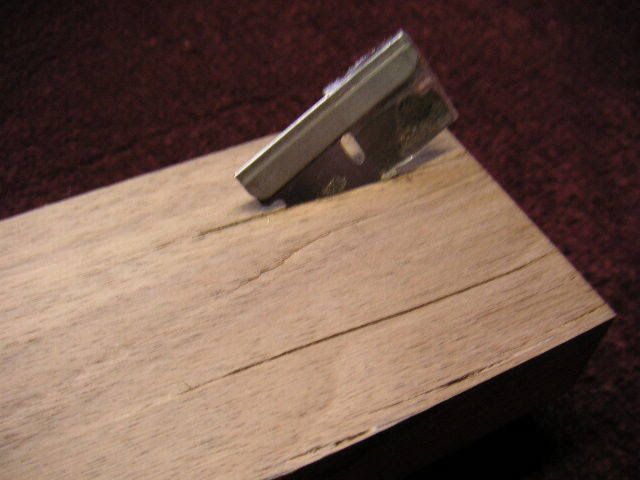
Subscribe to:
Posts (Atom)